Forged Carbon Dropouts
Share
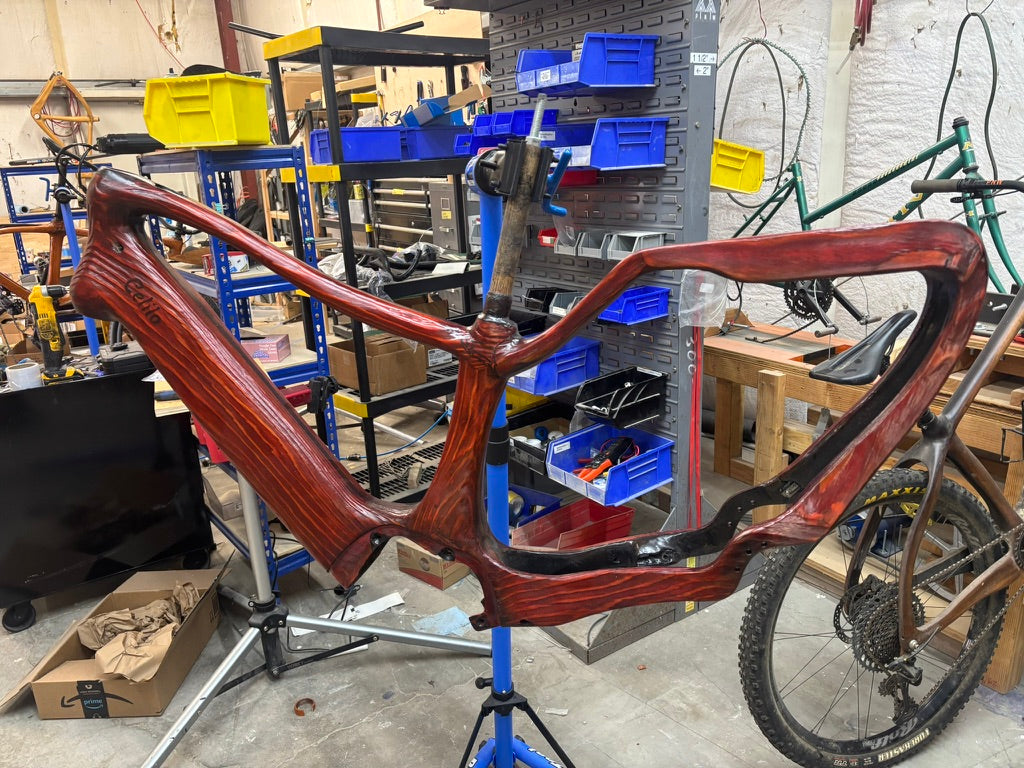
Forged Carbon and The Tricky Little Dropout
Most people don’t think about their dropouts. That’s fine-ideally, they do their job and never cross your mind again. But when you’re making bikes out of wood, your dropouts become one of those little design problems that turns into a multi-week saga. We’ve tried a lot of ideas over the years to get them just right-CNC machined aluminum, paragon dropouts, fancy bolts, hidden bolts, dovetails, epoxied sleeves, press fits. You name it.
Lately though, we’ve been experimenting with forged carbon, and it might be the first solution we’re genuinely excited about keeping around.
If you’ve never heard of forged carbon, you’re not alone-it’s a relatively new material in the bike world, and it’s bringing some pretty exciting possibilities to the table. It’s basically carbon fiber in play-dough form. Instead of laying sheets of woven carbon like you would with a traditional composite, forged carbon is chopped up, mixed with resin, and pressed into a mold under pressure and heat. It’s kind of the carbon fiber equivalent of casting metal.
And it turns out, for our purposes? It might be just right.
Why Even Bother?
Our wooden frames are stiff in the right ways and flexy in the others-something that makes a Celilo ride like nothing else. But when it comes to attaching your derailleur, axle, and brake, you don’t want flex. You want precise, strong, light, and tight.
Aluminum dropouts are great at this, but they require machining, bonding, and can be tricky to get just-so on a curved, machined wood surface. Forged carbon gives us a way to make custom-shaped parts that exactly match our frame, including internal hardware, bolt channels, and axle alignment. It’s also stronger than aluminum by weight, handles impact better, and doesn’t look half bad, either. Making our own parts also helps us address design constraints that are unique to wooden bikes, since the bolt or braze on designs that look slick on a steel bike with tiny stays don't always play nice with our designs.
Plus, unlike traditional carbon layup, we can prototype it fast. Press a new dropout design in an afternoon? Yep.
But is it actually strong?
Technically, forged carbon has a lower tensile strength than continuous-fiber composites, but for small, compact parts like dropouts, that’s not a problem. You’re not trying to span a canyon with these things-you just need them to hold tight and not twist when you sprint.
We mold ours with steel or brass inserts where needed, especially for threads, and the results are pretty stellar. They bond into the frame better than machined parts, they weigh less, and-crucially-they let us be way more creative in shaping the interface between wood and metal.
The Long-Term Plan
We’re not promising that every Celilo bike will use forged carbon from now on. But the more we work with it, the more we like it. It feels like it fits our whole vibe: creative, overbuilt, beautifully weird, and just a little bit obsessed with doing things the hard way-until suddenly, they’re the smart way.
So if you see a dark, marble-looking dropout on one of our bikes, now you know: it’s not plastic, it’s not metal, it’s not something you can buy off the shelf. It’s a tiny engineering victory, forged one dropout at a time.