
At Celilo, we are driven like salmon swimming upstream.
The salmon face obstacles—sea lions, fishers, slack water, waterfalls, and dams; but they push on as if it’s their only purpose, because it is.
Our mission is to create the best bike frames that even bike mechanics enjoy working on, may be less noble that that of the salmon (survival of the species), but we treat it as it’s our only purpose.
In order to make the best bike frame, we first need to decide what qualifies as ‘best’. While
for each rider that is a unique definition, for the purposes of this discussion let’s shorten the list to ‘it’s fun to ride’.
A frame that’s fun to ride is dependent on the riding condition. We at Celilo find the most reward from riding off-road, whether single track mountain biking or gravel grinding.
For mountain biking or gravel riding, before listing the desirable qualities let’s list some must nots:
- The frame must not fail under reasonably expected riding conditions
- The frame must not fail before a reasonable life expectancy
- The frame must not require extraordinary care and maintenance
So, what things do you want from your bike frame? Here are some must haves:
- Must look awesome (obviously)
- Must be appropriately rigid in the chain stay so all your watts go into the wheel, not bending
- Must be appropriately compliant in the front triangle so the frame absorbs the punishment
- Must dampen vibrations so your hands don’t go numb
These requirements point to a manufacturing method that allows tunability—something we can easily tweak to get high stiffness in some spots but compliance in others, while maintaining strength. For strength, and aesthetics, we need a method that allows for varying/organic cross sections.
These things point to composites manufacturing as the preferred manufacturing method. Composites can be easily tuned for strength and stiffness by varying reinforcement material (for example carbon fiber is very stiff and strong, where Kevlar is more compliant, but also strong), resin type (some resins are stiffer than others) and/or number of layers of reinforcement.
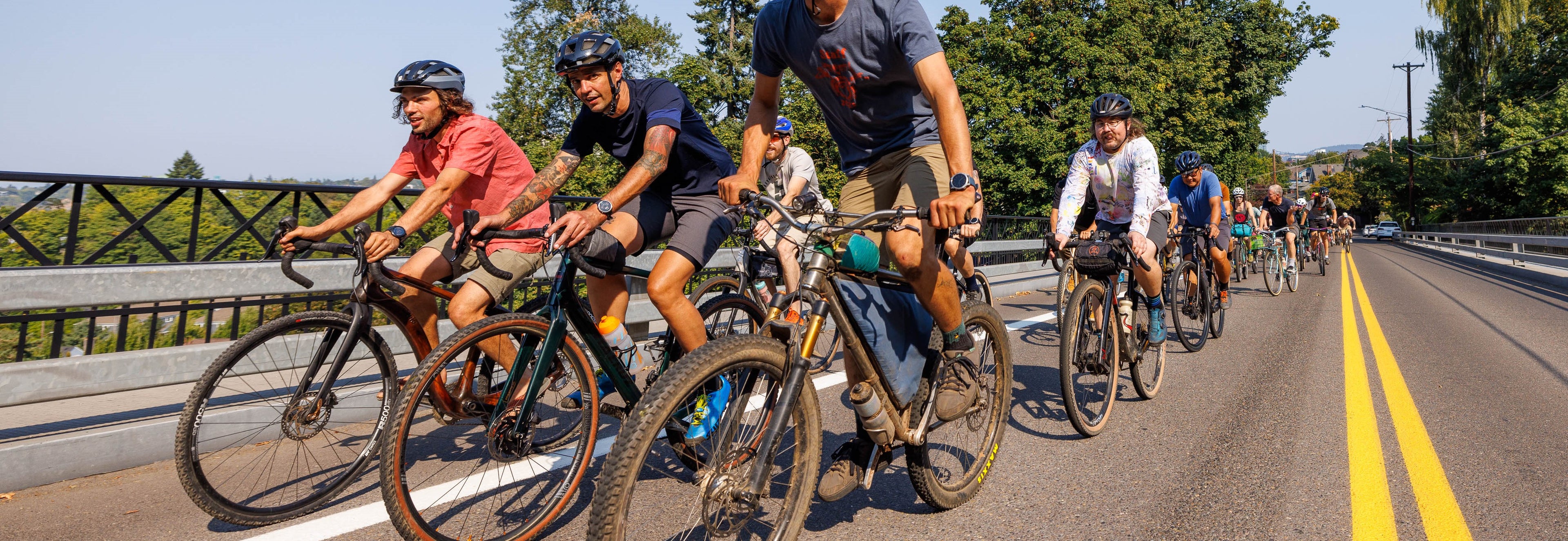
So why use wood? Why not just build composite bikes?
Excellent question!
For two of the items on the list above, wood is the hands down best material available—it looks awesome, and has excellent damping properties (it grew that way). Creating a wood/carbon/Kevlar structure results in a nearly optimal balance of strength, stiffness, compliance, and vibration damping. And wood just naturally looks awesome (though sometimes we enhance with stains and glazes).
Additionally, a knock on carbon bike frames (or generally) is that carbon fiber structures can be delicate, depending on the force loading scenario—for example rocks flung from the front tire to the down tube can be enough to pierce a carbon frame. Carbon is so strong in-line with the fibers that it doesn’t take many layers of fabric to provide the minimum tensile strength required of a bike frame. The thin walls can be problematic though (also true of metal frames). On Celilo frames the wood acts as a protective barrier to the structural carbon/Kevlar core.
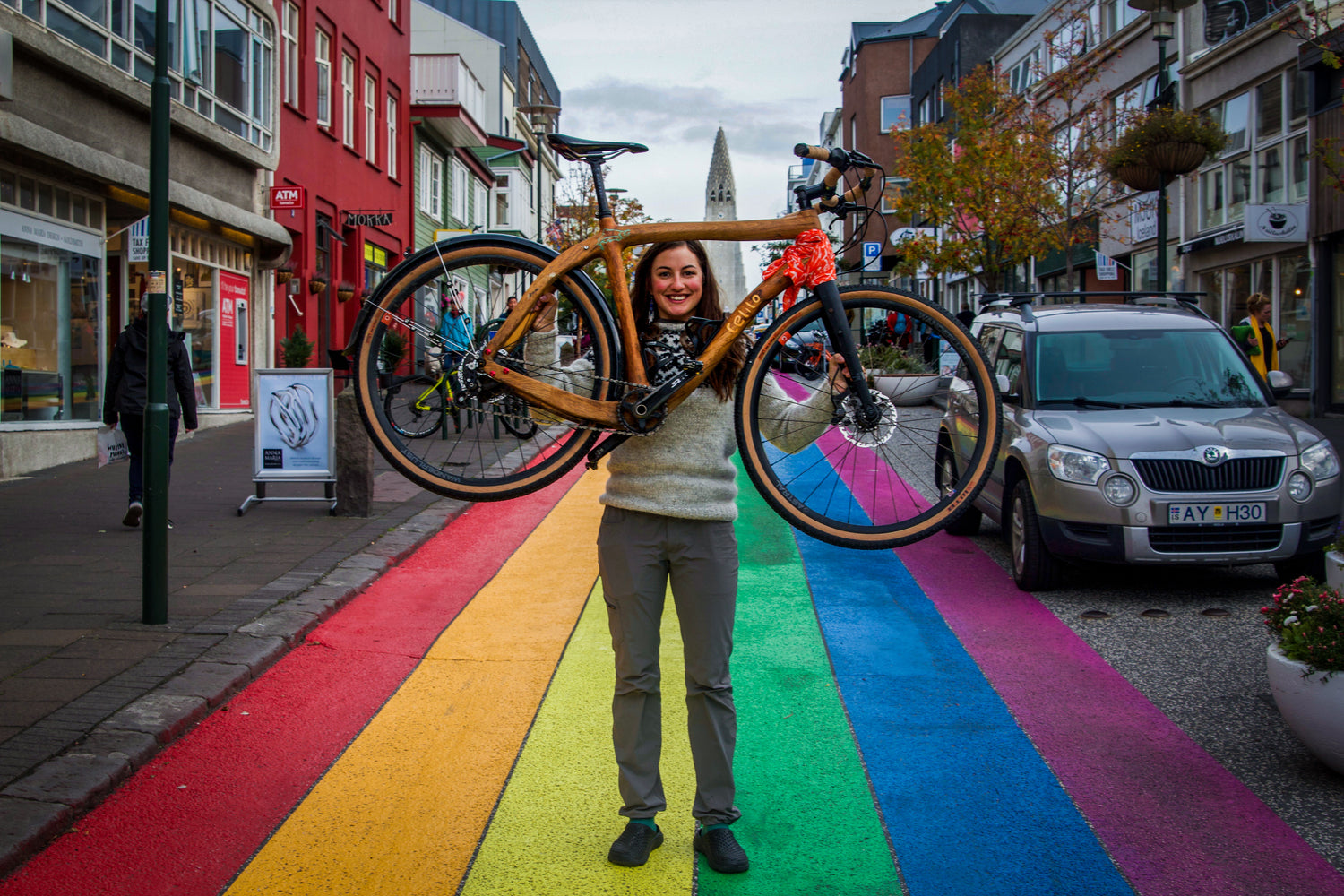
Why Mechanics Love Celilo Frames
The challenges with bike assembly are at the interfaces.
- Right dropout/derailleur hanger
- Left dropout/brake mount
- Bottom Bracket
- Seat post
- Headset
- Front derailleur hanger
- Cable routing
Starting from the top of the list, while we had some success with our own hanger design, we’ve recently made the switch to SRAM’s universal derailleur hanger (UDH). We’re pretty big fans of the direct mount strategy (no hanger required) and expecting it to trickle down through the SRAM line. The UDH interface allows for either direct mount SRAM or Shimano/SRAM hanger mount derailleurs.
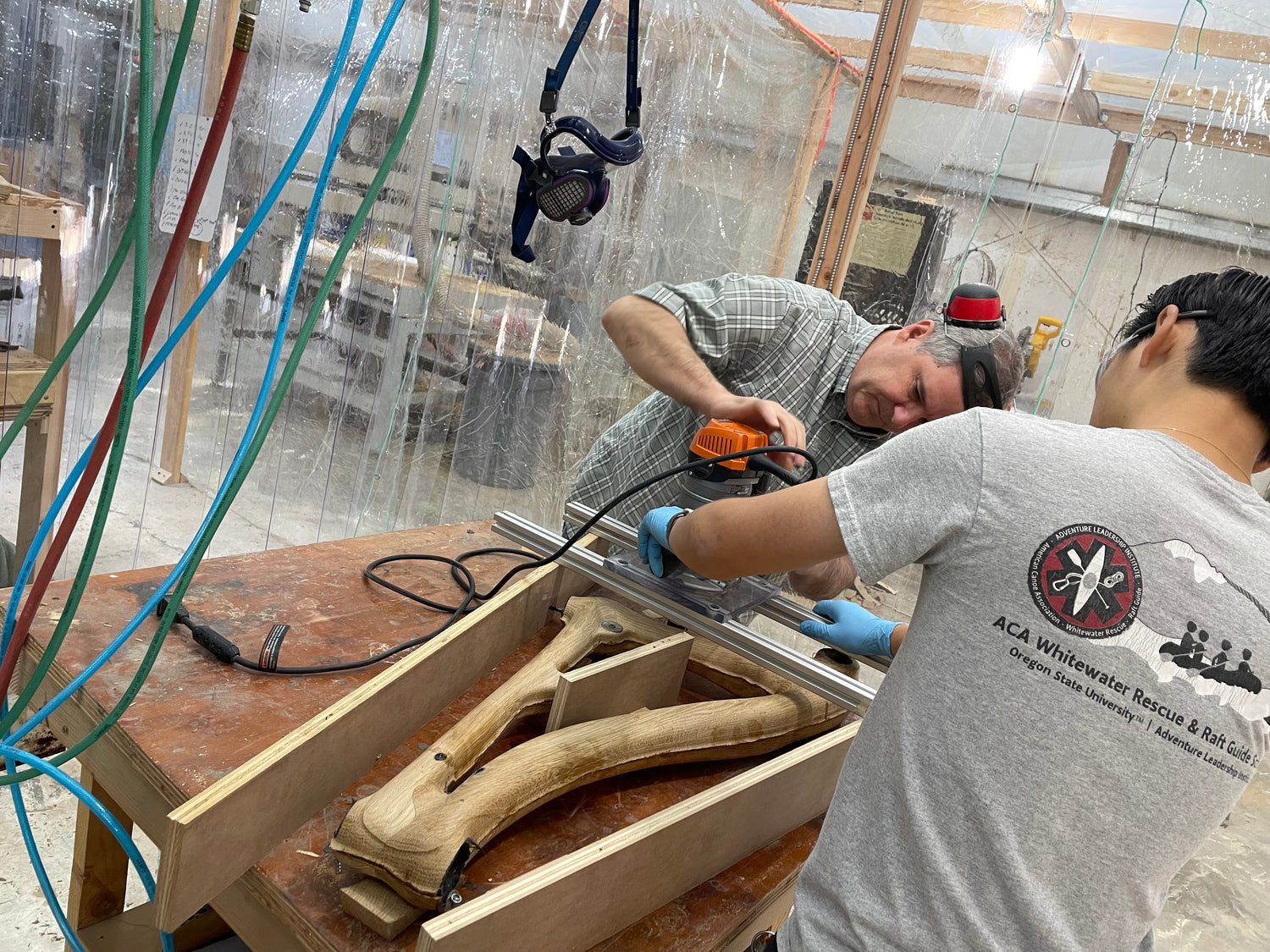
For our gravel bikes we like the clean looks of flat mount brakes. It’s taken a bit to develop the tools and fixtures to deliver a trued mounting surface that’s perpendicular to the axle, but the system now works great. For hardtails we’re designing around the ISO brake mount standard.
All of our frames are designed around dropper posts—haven’t been on many gravel or single-track rides where there wasn’t a time or two where dropping the saddle was the right play.
Since we’ve dedicated to droppers, we went all in—all of our frames have 31.6mm seat post diameter and have room for lots of dropper travel.
Our headset standard is ZS44/56—a tapered standard for 1 1/8” –1 ½” tapered forks that uses cups that press into the frame, and an easily replaceable bearing cartridge slips into the cups.
All of our gravel bikes are capable of running a front derailleur. We only install the hanger on request.
Cable routing—the vast majority of swear words expended when assembling our bikes have been due to cable routing issues. We are dedicated to the clean look though, and have developed some great strategies for providing clean routing paths.